Screw It with Titanium Head
Price $150.00
Product Details
Blade Length 4
Overall Length 3.75
Closed Length 5.25
Weight (oz) 1.1
Source From maker
Additional Specs
Knife Type Has Sheath
Blade Material Damascus
Blade Details Clip Point, Spear Point, Tanto
Handle Material Metallic, Wood
Other Details Tactical
About the Maker
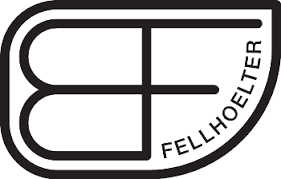
Fellhoelter, Brian
"I am a folder maker. While there will always be the occasional fixed blade, folders are my passion. The steels I enjoy working with include CPM154, ATS-34, 440C, S30V, and Stainless Damascus from Devin Thomas. All of the metal parts on my knives that can be Titanium are Titanium including frames, liners, thumbstuds, bolsters, clips and spacers. Pretty much everything except for the blade. I often anodize a substantial portion of my titanium, and can get a deep green that few makers succeed at. As far as handle materials go, I mostly use Carbon fiber, G10, or Micarta. I use large bronze pivot bushings in all of my folders, and either Nylatron or Bronze washers. All of my parts are made in-house except the screws. I have an old Bridgeport Mill, an older Logan Lathe (1943), a Hardcore grinder, and various other tools, lots of them made by myself. I also do all of my own Heat treating in an EvenHeat Oven." My knives have won several major awards, including Best Tactical Folder at the Blade Show 2011.
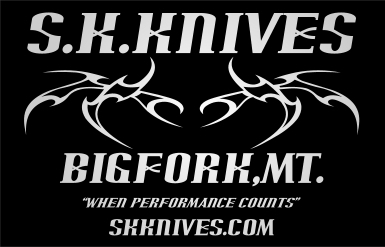
Kelly, Steven
S.K. Knives is located in Bigfork, Montana. "I built my first knife in 2000. I was determined to create my own hunting knife. Even before it was finished, I had realized that I had been bitten by the knife making bug. Soon after that fist knife was finished, I began building the knife I carried while performing my duties, as a Deputy Sheriff. Before long I was building knives for friends, relatives and co-workers. In 2001 I was introduced to the forge. I have been forging blades ever since. In late 2002 I began building my own Damascus. I did it the old fashioned way, using a variety of hammers and a 125 lb anvil. I learned many valuable lessons by building my Damascus this way, but was relatively limited in my pattern capabilities. In April of 2005 I completed my 50 ton hydraulic forging press and am now making an array of mosaic Damascus patterns. In June of 2008 I successfully passed my American Bladesmith Society, Journeyman Smith test. This accomplishment completed the next step in my continuing quest of making myself the best knife maker I can be. In 2009 I decided to fall back on my roots from 15 years of Law Enforcement experience. I began building more tactical style knives with a strong focus on folders. And an emphasis on what I would carry if I was still working the streets. Most of my tactical knives and folders are built with CPM-154 stainless blades, Titanium and composite handle materials. I fully believe in and use the designs I produce. My knives are used in and subjected to one of the toughest environments in the Country, the Montana outdoors. Montana has some of the most severe weather challenges and the best sporting challenges anywhere. My knives have stood up to the challenges time and again. I also perform regular testing on the knives I build. Because of this philosophy, I limit myself to using a select few steels, that I have tested, time and again. Most of my straight steel working knives are built from 52100 or 1084 tool steel. I also use other steels such as CPM-154 when the need and function of the knife require a stainless steel blade. I build the majority of my straight laminate Damascus patterns from 1084 or 1080 and 15n20 with the occasional addition of that something special for added effect. I also build a variety of canned Damascus patterns which incorporate several different steels and shapes. This process provides some of the most unique and diverse patterns imaginable. I am very proud of the fact that I can claim sole proprietorship of my work. I do all of the work that goes into my knives. I perform all of my own heat treating, with differential edge quench being my choice for the majority of my knives. I am convinced that this provides the best combination of edge holding ability and toughness in most applications."
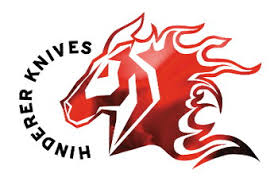
Hinderer, Rick
In the mid 1980’s Rick Hinderer began his knife making journey making art knives in a small 14′ x 18′ turkey coop with none of the modern amenities, like heat or running water! Art knives are a far cry from the tactical scene which Rick is so deeply entrenched in now. Over the years his meticulous attention to knife design and knife making, coupled with his real world experience as a Fire Fighter / EMT sets him apart from the rest. Rick’s design philosophy is deeply rooted in his experience with using his knives as part of his first responder tools. That catalyst of change from art knives to hard use tactical was after Rick joined the rescue dive team. He really began to look at knives and designs more as hard use tactical tools than works of art. Rick began changing over from old world knife making techniques to modern CNC precision manufacturing. With the combination of designing art knives, and his real world experience as a first responder, this unusual perspective allows him to design hard use tactical folders that are not only aesthetically pleasing to the eye, but extremely comfortable in the hand. All of Rick’s products are engineered to go the distance when it counts the most whether it be when life is on the line, or you just need a good cutting tool.